Prozesstechnologie
Die Prozesstechnologiegruppe arbeitet an der Weiterentwicklung industrieller Herstellungsprozesse für mono- und multikristalline Siliziumsolarzellen. Hierzu werden neue Konzepte und Technologien erforscht, sowie zum Teil bis zur Pilotlinienreife entwickelt, um sie in die industrielle Anwendung zu überführen. Die Auswahl der verfolgten Konzepte orientiert sich dabei an der kurz bis mittelfristigen industriellen Umsetzbarkeit und dem Potential einer Kostensenkung photovoltaischer Stromerzeugung durch eine Wirkungsgradsteigerung oder eine Reduktion der Herstellungskosten. Ergänzt wird diese anwendungsorientierte Arbeit durch Forschungsaktivitäten, die ein vertieftes Verständnis der physikalischen Vorgänge einzelner Prozessschritte zum Ziel haben.
Solarzellenkonzepte

Selektiver Emitter
Eine Reduzierung der frontseitigen Rekombinationsverluste kann durch einen selektiven Emitter erreicht werden. Dabei wird nur der metallisierte Emitter-Bereich hoch dotiert, um einen geringen Kontaktwiderstand zu gewährleisten, während die beleuchtete Oberfläche zur Reduzierung der Rekombinationsverluste nur schwach dotiert wird. Ein dazu in der Industriesolarzellengruppe entwickelter Rückätzprozess wird derzeit vom Anlagenhersteller Gebr. Schmid GmbH vermarktet.

Passivierte Zellrückseite
Zur Reduzierung der Rekombinationsverluste an der Zell-Rückseite kann das vollflächige Aluminium Back-Surface-Field (BSF) einer Standard-Solarzelle durch eine dielektrische Passivierung ersetzt werden. Diese wird zur Kontaktierung der Rückseite lokal geöffnet und vollflächig mit Aluminium-Paste bedruckt. Während des Feuerns bildet sich in den geöffneten Bereichen ein lokales Back-Surface-Field und sorgt so für eine Feldeffektpassivierung der hoch rekombinationsaktiven Kontaktfläche.
Zur Oberflächenpassivierung durch Aluminiumoxid steht eine Oxford ALD-Anlage (Atomic Layer Deposition) zur Verfügung, als kostengünstige Alternative ist zudem eine Abscheidung mittels der APCVD-Technologie (Atmospheric Pressure Chemical Vapour Deposition) Gegenstand der aktuellen Forschung in der Industriesolarzellengruppe.
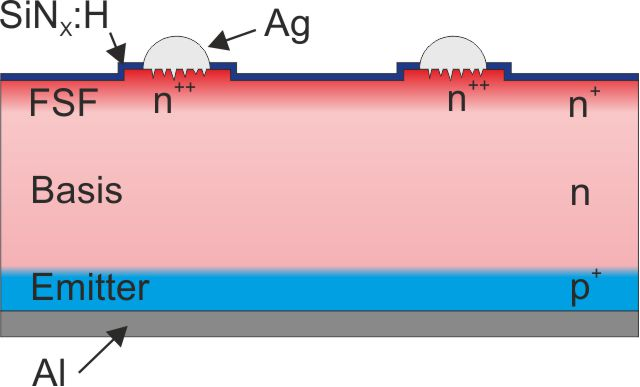
n-Typ Solarzellen
Die Rekombination in der Basis stellt für Standard-Solarzellen eine der Hauptverlustquellen dar. Die erfolgreiche Optimierung der Einzelprozesse in den vergangenen Jahren lässt den Anteil der Basis-Rekombination an den gesamten Verlusten weiter steigen, zudem stellen zukünftige Zellkonzepte teilweise deutlich höhere Anforderungen an die Qualität des Basis-Substrats. Das derzeit für die große Mehrzahl industriell gefertigter Solarzellen verwendete p-Typ Silizium weist eine Minoritätsladungsträger-Lebensdauer von typischerweise deutlich unter 1 ms auf. Unter Beleuchtung bilden sich rekombinationsaktive Bor-Sauerstoff-Komplexe, die zu einer lichtinduzierten Degradation der Minoritätsladungsträger-Lebensdauer führen.
Deutlich höhere Minoritätsladungsträger-Lebensdauern können durch mit Phosphor n-dotiertes Cz-Silizium erreicht werden, welches eine geringere Sensibilität für metallische Verunreinigungen aufweist, und aufgrund des sehr geringen Bor-Gehalts kaum von der lichtinduzierten Degradation betroffen ist.
Das sogenannte PHOSTOP-Zellkonzept stellt die einfachste Möglichkeit dar, eine auf n-Typ Silizium basierende Solarzelle herzustellen. Der Zellprozess entspricht weitgehend dem einer Standard-Solarzelle, die n-dotierte Basis wird dabei frontseitig durch das Phosphor-Front-Surface-Field passiviert, während die Einlegierung von Aluminium auf der Rückseite zu einem p/n-Übergang führt, an dem die Ladungstrennung erfolgt. Der geringere Rekombinationsstrom in der Basis führt zu einem Anstieg der offenen Klemmspannung, außerdem trägt die n-leitende Basis zur Querleitfähigkeit zwischen den Front-Kontaktfingern bei und erhöht damit den Füllfaktor. In Verbindung mit einer verbesserten Frontseitenpassivierung wurden mit diesem Zellkonzept Wirkungsgrade von bis zu 19,5% auf großflächigem Cz-Silizium an der Universität Konstanz erzielt.
Bifaziale Solarzellen
Bifaziale Solarzellen weisen eine passivierte Rückseite auf, die durch eine der frontseitigen Metallisierung ähnliche Fingerstruktur lokal kontaktiert wird. Da nur die kontaktierte Fläche mit Metall bedeckt ist, kann eine solche Zelle von beiden Seiten Licht absorbieren. Bei geeigneter Aufstellung kann so über einen Tag hinweg bis zu 20 % mehr Strom produziert werden. Eine senkrechte Aufstellung führt bei Ost-West-Ausrichtung der Oberflächen zu einer Umverteilung der Stromerzeugung auf den Vor- und Nachmittag und kann so dazu beitragen, den „Mittags-Peak“ des in das Stromnetz eingespeisten Solarstroms auszugleichen.
Neben der Passivierung der rückseitigen Zell-Oberfläche weist eine bifaziale Solarzelle darunter üblicherweise ein Dotierprofil mit der umgekehrten Polarität der frontseitigen Dotierung auf. Dieses dient der Verbesserung der Querleitfähigkeit und des Kontaktwiderstands, außerdem trägt das damit verbundene elektrische Feld zur Passivierung der Oberfläche bei. Bifaziale Solarzellen können aus p- oder n-Typ Silizium hergestellt werden, je nach Polarität der Oberflächen-Dotierung befindet sich der Emitter auf der Front- oder Rückseite der Solarzelle.
Aktuelle Forschungsaktivitäten der Industriesolarzellengruppe zu bifazialen Solarzellen konzentrieren sich auf die kostengünstige, möglichst gleichzeitige Erzeugung der Dotierprofile sowie die Reduzierung von Rekombinations- und Serienwiderstandsverlusten bei der Kontaktierung Bor-dotierter Oberflächen.
Prozessierung von Solarzellen
Die Prozessierung von Solarzellen erfolgt mittels industrieller, prototypischer und selbstgebauter (Groß-)Maschinen. Diese, das Herzstück der Infrastruktur ausmachenden Gerätschaften, werden in vielfältiger Art und Weise bei der Bearbeitung der Roh-Wafer bis hin zur Kontaktierung der fertigen Solarzelle eingesetzt. Die dabei eingesetzte Technologie entspricht höchsten Ansprüchen, wie sie im fortschrittlichen Sektor der Photovoltaik eingesetzt wird.
Die Prozessierung jeglichen Typs von Solarzelle beinhaltet dabei eine unterschiedlich große Anzahl von Prozessschritten, die in variabler, aber auf das Si-Material und den zu prozessierenden Solarzelltyp abgestimmter Weise, hintereinander zur Anwendung kommen.
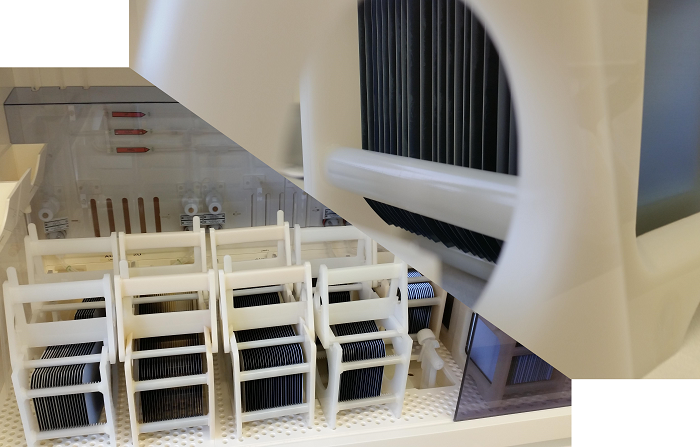
Reinigung und Oberflächen-Topografie
Zu Beginn jedes Solarzellenprozesses steht die Konditionierung des Roh-Wafers. Dazu wird jede Silizium-Scheibe je nach Ausgangsqualität, Materialtyp und Oberflächenzustand einer Folge von nasschemischen Ätzschritten unterzogen, die es zum Ziel haben, die Oberfläche des Wafers von der maximal möglichen oder nötigen Menge an Verschmutzungen (Metalle und Organika) zu befreien. Hintergrund ist die Verhinderung der parasitären Eindiffusion von potentiellen, Defektzustände generierenden Verunreinigungen in das Silizium-Volumen in den folgenden Prozessschritten, wie z.B. die gezielte Hochtemperatur-Eindiffusion von Dotanden.
Neben der Reinigung, die in unterschiedlicher Weise und mit unterschiedlichster chemischer Zusammensetzung geschehen kann (HF/HCl-Lösung; H2SO4/H2O2-Lösung; etc.), kann bei der Ätzung der Silizium-Oberfläche auch eine Änderung der Oberfläche in gezielter Weise geschehen. Dieser, als Texturierung bezeichneter Vorgang, wird durch alkalische oder saure Ätzlösungen hervorgerufen und resultiert in einer Kristallorientierungs-abhängigen Oberflächenstrukturierung, die einer inversen Pyramiden- bzw. ineinander verschlungener Wurm-Struktur ähnelt. Diese Topografieänderung trägt später zur Reflexionssenkung und Effizienzerhöhung bei, benötigt wegen der vergrößerten Oberfläche aber auch eine qualitativ hochwertige Oberflächenpassivierung.
Dotanden-Diffusion und Oberflächenpassivierung
Direkt nach der Reinigung werden die Wafer in einem Rohrofen mittels eines Hochtemperaturschrittes dotiert. Die notwendige Dotierquelle kann dabei in situ aufgewachsen oder vorbeschichtet sein. Am Ende entsteht der notwendige pn-Übergang im Silizium-Volumen, der zur Ladungsträgertrennung in der Solarzelle führt. Bei der Eindiffusion kommt es als Nebeneffekt auch zum Getter-Effekt von Verunreinigungen im Si-Volumen, wodurch die Qualität des Materials erhöht wird. Zur Erhaltung dieses Reinzustandes und zur Absättigung verbleibender offener Silizium-Bindungen wird durch Aufbringung von meist dielektrischen Schichten die Oberfläche des Wafers versiegelt. Dabei werden auch hochwertige und multifunktionale Schichten verwendet, die zusätzliche Eigenschaften, wie z.B. die Verminderung der Reflexion, eine erhöhte Passivierqualität und/oder eine Kontaktierungs-unterstützende Wirkung aufweisen. Letztere werden primär in CVD-Reaktoren abgeschieden, in denen Gase unter Plasmaeinwirkung zur Abscheidung von Feststoffen eingesetzt werden.

Metallisierung
Der finale Schritt bei der Prozessierung von Solarzellen stellt die Kontaktierung der unterschiedlich dotierten Bereiche auf der Oberfläche dar. Dazu werden herkömmliche und industriell als Standard verwendete Siebdruckverfahren, aber auch in der Entwicklung befindliche Techniken angewandt. Am Ende kommt ein meist metallischer Kontakt zwischen dem dotierten Halbleitermaterial und einem im Modul verschaltbaren Stoff zustande. Im Falle von Metallpasten wird der Kontakt zur Siliziumoberfläche dabei mittels eines weiteren Hochtemperaturschrittes in einem Gürtel-Durchlaufofen realisiert.
Technologie
Zur Abbildung all dieser Standard bis hoch-experimentellen Prozessschritte und -sequenzen wird neben einem großen Fuhrpark an Maschinen auch eine entsprechende Versorgungsstruktur benötigt. Besonders im Falle der hiesigen Verknüpfung von Grundlagenforschung und industrienaher Prozessführung zur Entwicklung von Solarzellkonzepten ist ein sehr variabler Maschineneinsatz bezüglich möglicher Parameter, wie auch die Flexibilität zur Gestaltung neuer Prototypen und Selbstbauten notwendig. Gerade die in Zusammenarbeit mit der Industrie geplanten und umgesetzten Anlagen werden kontinuierlich erneuert und verbessert.

Prozessequipment
Der Fuhrpark zur Prozessierung setzt sich primär aus Großgeräten zusammen, die manuell bis vollautomatisch bei der Prozessierung eingesetzt werden. Je nach Maschine liegt dabei der Durchsatz vom Einzelwafer, wie er in der Forschung verwendet wird, bis hin zum industriellen Durchsatz von mehreren hundert Stück je Stunde, zur Abbildung von realen Bedingungen. Einige dieser Großmaschinen sind beispielhaft gelistet:
- Nasschemische Prozessierbänke
- Rohr-Diffusionsofen
- Elektronenstrahl-Verdampfer und Sputter-Anlage
- Nano- und Pikosekunden Lasersystem-Maschinen
- RTP und Anneal-Öfen
- PECVD-, ICP-PECVD-, APCVD- und ALD-Anlagen
- Siebdrucklinie (Siebdrucker und Trockenofen)
- Gürtelofen
- Inkjet-System
- Chip-Säge
- Porosizieranlage
- Diverse großformatige Charakterisiersysteme (ICP-OES, GD-OES, REM, etc.)
Darüber hinaus gehören zur Infrastruktur die Aufrechterhaltung der Funktion der Maschinen, d.h. die Wartung und Reparatur der Anlagen, sowie die Versorgung mittels Medien (Wasser, Kühlwasser, DI-Wasser, Druckluft, Stickstoff, Sondergase, Strom und sonstige Verbrauchsmittel). Besonderes Augenmerk liegt zudem auf der Arbeitssicherheit, insbesondere beim Einsatz von Sondergasen wie zum Beispiel in CVD-Systemen.